Notre différence, c'est l'intégration. Elle réside dans le fait que pour chacun de nos projets, notre valeur ajoutée est dans l’intégration des composants des solutions mises en œuvre, mais aussi de « thèmes complémentaires » qui feront la réussite de vos projets. Cette intégration à 360° est possible parce que nous avons rassemblé dans le groupe FRV toutes les compétences nécessaires à la réussite de vos projets au travers de nos 4 filiales.
Philippe FALAISE
Découvrez nos 7 processus industriels qui structurent notre savoir-faire
Process de transfert de matières
Transférer des matières premières, des produits intermédiaires ou des produits finis selon les différentes phases de production nécessite une attention particulière selon les caractéristiques du produit.
Nous sommes amenés à prendre en compte les caractéristiques du produit à transférer pour choisir le système de transfert à mettre en œuvre (le mode et les conditions) :
- Les modes de transfert du produit en remplissage et en soutirage (gravitaire, pompage, aspiration par le vide, dosage, etc.).
- Les conditions de transfert : chaud/froid /anaérobie/pousse à l’air ou gaz neutre.
Process de dosage et de mixage
Le dosage des produits liquides ou semi-pâteux par procédés divers avec asservissements et contrôles nécessite des technicités spécifiques en fonction du pH (de pH3 à pH12).
Notre expertise nous amène à traiter le choix de l’hydraulique correspondant au produit véhiculé (par pompe doseuses, par pompe volumétrique, par pompe à piston, par aspiration par le vide ou par débimétrie) et le type de dosage (par batch, par micro dosage).
Concernant le mixage des mêmes produits, notre expertise nous amène à travailler aussi sur le choix du mode de mixage (par injection, agitation statique ou dynamique, blender hydroéjection, etc.).
Process d'échange thermique
Sur les sites de nos clients, nous nous posons la question : Quel type d'échangeur ? Tubulaire ou à plaque ?
Cela dépend de l’échange thermique à réaliser, la nature des produits à véhiculer et du secteur d’activité dans lequel l’échangeur va être intégré (alimentaire, pharmaceutique, chimique…etc.)
En fonction de ces critères, notre expertise nous amène à réaliser l’étude, la définition, la configuration de l’échangeur et de son environnement technique (vannes de sectionnement, vannes de régulation, sonde de température, capteur de pression, poste de purge, etc.) ainsi que la mise en adéquation de l’ensemble de ces composants sans oublier le pilotage du fonctionnement de l’ensemble.
Process de stockage
Les paramètres entrant dans les conditions de stockage de produits, qu’ils soient liquides ou semi-pâteux sont différents selon leur pH (de pH3 à pH12).
Notre expertise nous amène à traiter les sujets suivants :
- Identification du process concerné.
- Caractéristiques du produit (viscosité, densité, sensibilité, applications, etc.).
- Conditions de stockage: chaud/froid/ agité/en circulation en boucle fermée, etc.
- Contrôles du stockage: niveau/poids/volume transféré.
- Protection des produits sensibles par inertage (7N ou CO2) contrôlé et régulé.
Process de traitement de l'eau
Eaux pharmaceutiques (EPU, EPPI) , eaux minérales, eaux déminéralisées… Autant d’eaux très différentes qui nécessitent des traitements, des stockages, des distributions et des utilisations spécifiques.
Selon le type d’eau à traiter, notre expertise nous amène à mettre en œuvre des solutions spécifiques :
- Postes d’adoucissement
- Ultra Filtration/Osmose
- Ozonation
- Station de déminéralisation
- Stockage et distribution d’eau purifiée, d’EPPI
- Traitements d’eau minérales naturelles
- Installations de TAR, etc.
Process de nettoyage (CIP/NEP)
Les conditions de nettoyage dépendent beaucoup des produits transformés, des conditions de stockage et de distribution.
Selon ces conditions, notre expertise nous amène à mettre en œuvre des solutions différentes :
- Stations de NEP complètes intégrant cuverie, pompes d’envoi et pompe de retour, mesure de conductivité, poste vapeur, retour condensats, poste d’injection des réactifs, poste de dilution des réactifs, armoire de contrôle /commande, liaison sur site pour pilotage à partir d’un process existant.
- Réseau de NEP dédié (qui va véhiculer la solution soude/acide). Au final des mesures de conductivité vérifient la qualité du lavage.
Process de gestion du réseau vapeur
La vapeur est un fluide caloporteur très répandu dans l’industrie parce qu’elle présente de grands avantages : excellent fluide caloporteur, chaque kg de vapeur peut transporter une grande quantité de chaleur, comparée à l’eau chaude, l’eau surchauffée et l’huile thermique, la vapeur est le fluide qui présente le coefficient de transfert thermique en paroi le plus élevé.
Mais, la vapeur présente aussi quelques désavantages, en particulier : C’est un fluide cher : environ 40 à 70 €/tonne vapeur (2016)! Ce coût intègre celui du combustible utilisé dans la chaudière, mais aussi le prix de l’eau et le coût de son traitement.
C’est la raison pour laquelle le groupe FRV met toute son expérience pour optimiser la production de vapeur, sa distribution et sa consommation.
Cette optimisation peut se faire soit par :
- l’assistance aux acteurs de la vapeur (contrôle purgeur, audit réseau, conseils de montage, audit énergétique, formation, etc.
- La conception de vos équipements (poste de détente, poste de purge ligne, pompe condensats, ballon flash, collecteurs, préparateurs d’eau chaude, etc.
- La fourniture de matériel (composants ou sous forme d’ensemble-skids) qu’il s’agisse de robinetterie, de pompes, d’instrumentation ou d’accessoires.
Nos experts vous retranscrivent une actualité complètement industrielle
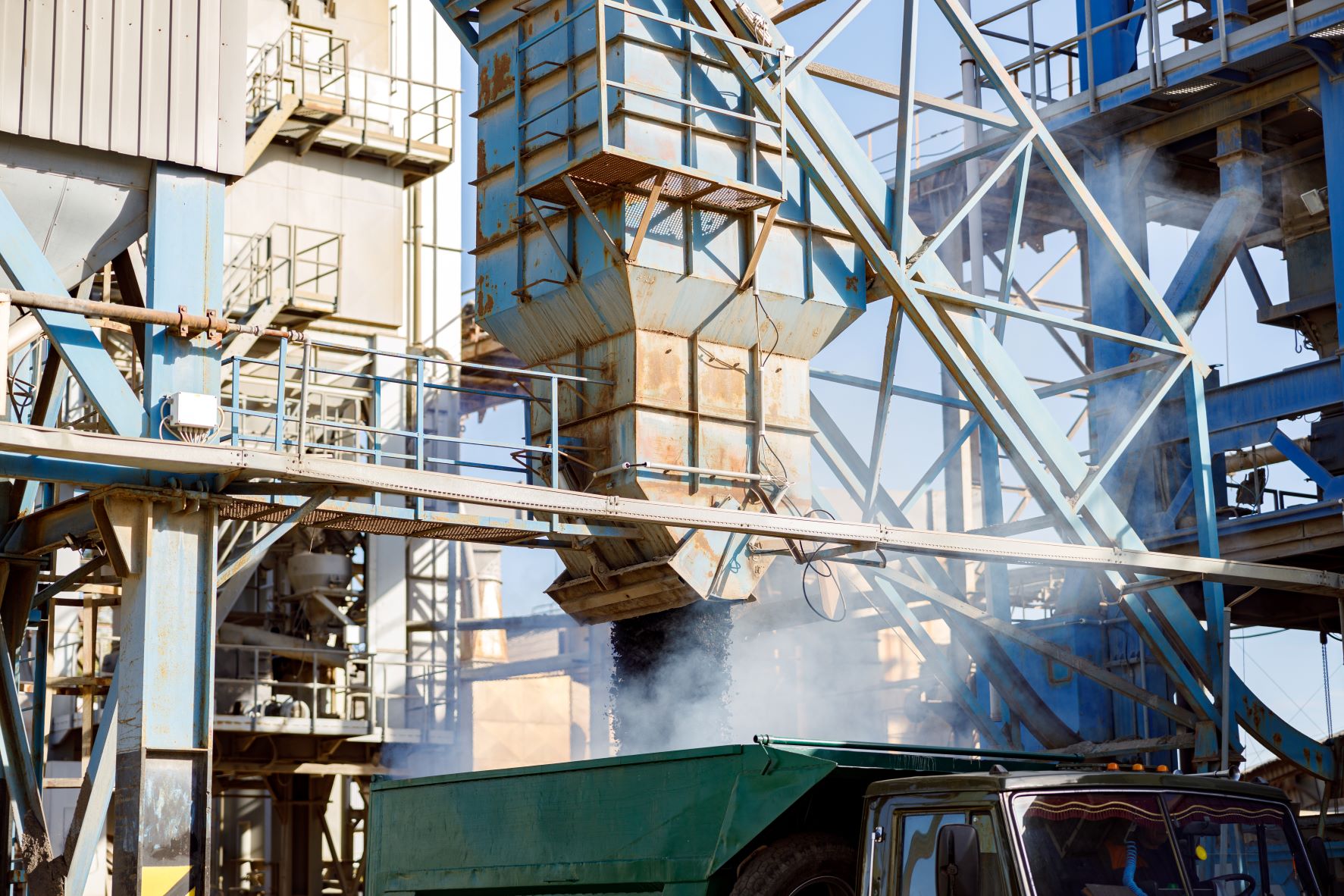
Le pompage industriel : une expertise complète pour l’optimisation de vos installations
Le pompage industriel : une expertise complète pour l’optimisation de vos installations En savoir plus
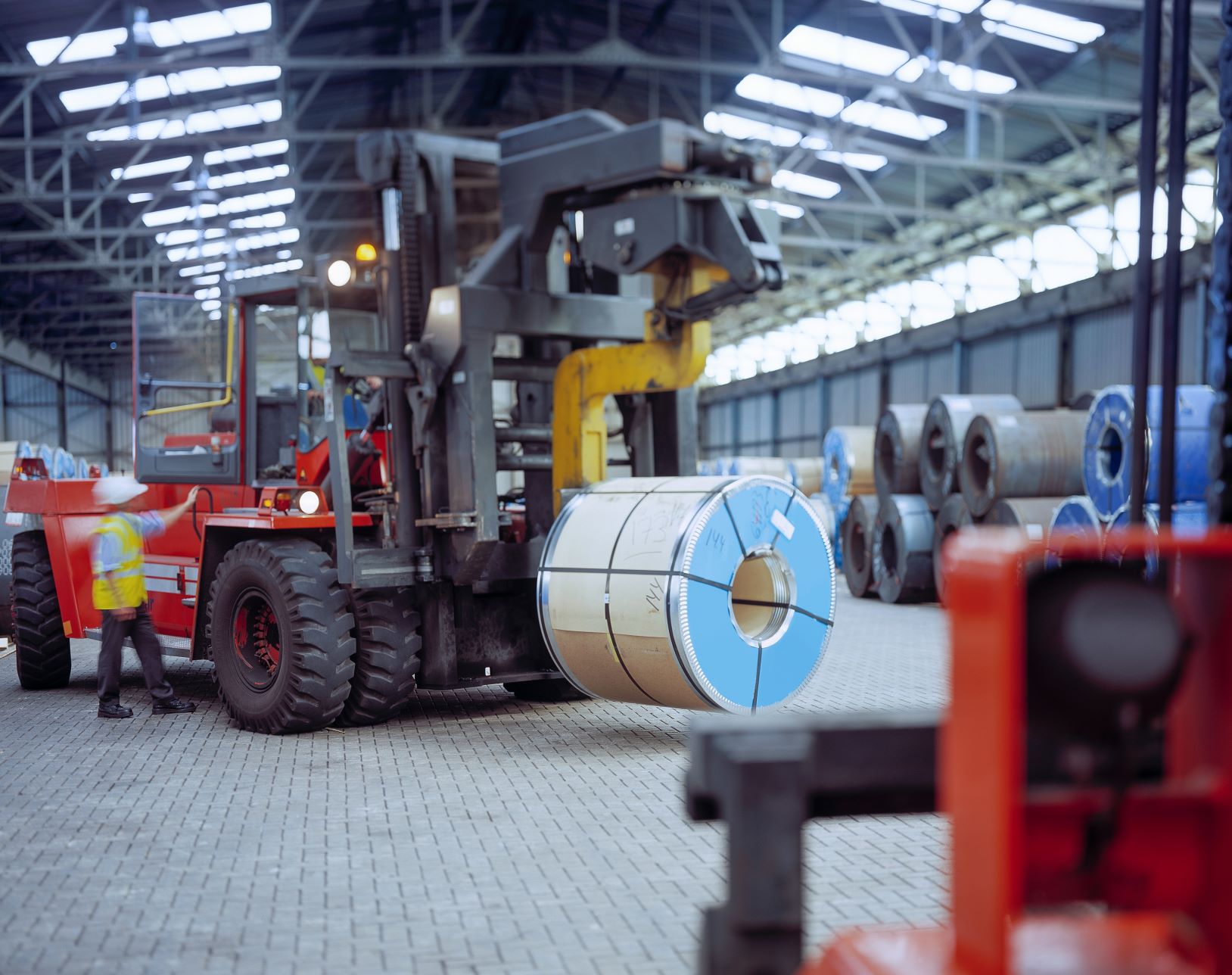
Le groupe Getmore: pourquoi nous faisons la différence ?
Le groupe Getmore: pourquoi nous faisons la différence ? CONTACT Dans le En savoir plus

Des solutions sur mesure pour l’industrie agroalimentaire
Des solutions sur mesure pour l’industrie agroalimentaire CONTACT L’industrie agroalimentaire est un En savoir plus